ATC’s Lean Journey
Here in ATC we have begun our Lean journey. We have begun this journey to help us transform the way we serve our customers. We feel that customers are central to our success as a company, and we aim to develop our entire business around the continuous effort to deliver the best experience possible. It is this that drives us to improve our customer experience, by figuring out how to deliver faster, more cost effectively, and with the best quality. Our lean program is key to us succeeding here.
Our journey initially starting with weekly stand up meetings at which all staff were invited to note their ideas for improvements or any issues causing frustration. More than 100 ideas and issues have been generated in this way. Of these, all with the exception of one have been actioned or closed out. These weekly stand-up meetings have had different themes including making staff aware of the 8 wastes (TIM WOOD), 5S and 5 Whys.
We are now delighted to announce our next step in our commitment to lean, and improving our customer experience. Four of our team recently commenced their Lean Green Belt training with LBS Partners. The Lean Business Green Belt programme will include the completion of in-company projects. The purpose of the training is to develop a clear understanding of Lean tools and practices such that participants have the know-how to implement same. The team will then bring back these skills, and help apply them in their day to day jobs to continue the drive to the ultimate customer experience.
Approach
Our visual management centre which is the location for team member ideas and issues. Weekly stand-up meetings are carried out here. Visual management boards for tracking projects and issues
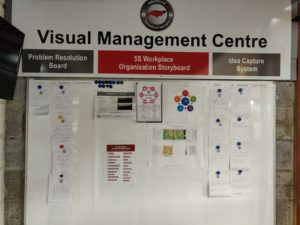
Visual Management Centre
Examples of some improvements include a FIFO rack for parts regularly used in our processes.
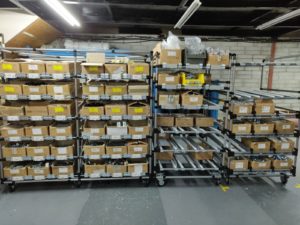
FIFO Racks
And an Action Tracker Board gives us greater visibility on the progress on projects.
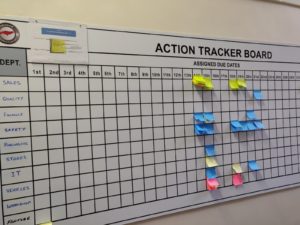
Action Tracker Board
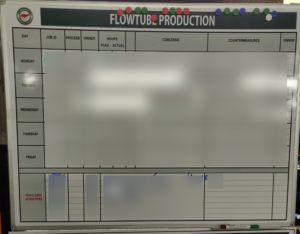
Action Tracker Flowtube
Other improvements include stand-up tables for staff, shadowboards, labelling and kanban processes for managing stock and using visuals such as a sheet of coloured paper to indicate the paper needs to be refilled in our printers.
Continuous improvement continues to be a driving force for us as we continue our Lean journey. A journey that has only just begun.